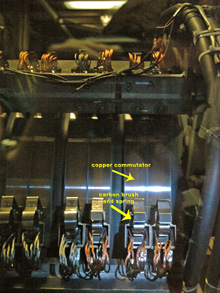
The common way to supply electricity to the armature (the part that rotates) of the motor is through a series of carbon brushes that rub on a copper surface known as the commutator. These brushes started bouncing on the commutator, damaging the brushes and wires before a spring broke and started to damage the commutator. Thompson engineers secured and repaired the motor, fixing a problem that potentially could have sent the ship back into port for repairs. Click image for larger view and image credit.
Two Major Problems
December 26, 2005
Kelley Elliott
Web Coordinator
NOAA Office of Ocean Exploration
Chief Engineer
RV Thompson
Two near catastrophic problems harboring the potential to send the ship back to port occur at once. Brushes supplying electricity to the starboard propulsion motor bounce out of control before springs brake and begin damaging parts of the motor that generate the electricity used to turn the motor. The problems compound as a magnetic sensor on the WHOI Dynacon winch, necessary for DSL120 operations, fails.
First, problems with the starboard propulsion motor arise. The armature of the motor (the part that rotates) is always turning, so the common way to supply electricity to the turning armature is through a series of carbon brushes that rub on a copper surface known as the commutator. These brushes are held at a precise distance from the commutator and are pressed onto the commutator by springs keeping a uniform tension on the brushes.
The problem with the starboard motor began when these brushes started bouncing on the commutator. Since the carbon material is very fragile, the brushes and the wires attached to them become damaged very quickly. The situation becomes worse to the point where the movement of the brushes breaks some of the springs. A piece of broken spring is caught under a brush and starts to damage the copper commutator.
We secure the motor, clean the commutator with a stone (similar to a knife sharpening stone) and replace brushes and springs as needed to alleviate the problem. Although we are still not sure exactly what caused the problem, we are able to repair the damage and replace broken parts. The motor is back in service and functioning well.
And if the problems with the starboard propulsion motor are not enough, as technicians in the DSL van take up some of the thousands of meters of cable paid out to the DSL120 currently under tow, they notice a winch malfunction. The cable being wound onto the winch is not aligning properly, so instead of wrapping cleanly next to the existing cable, the new cable is laid at an awkward angle that could cause tangles in the wire. The winch has a number of sensors on it designed specifically to bring the cable back around the winch in a neat and orderly fashion, like the level-wind on a fishing reel.
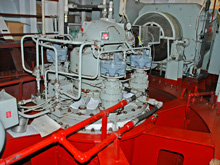
RV Thompson has two 3000 horse power, DC electric motors, each run by 750 volts or 3150 amps of electricity. The motor is driven around by a magnetic flux created when electricity, generated by the main diesel engine, is run through the armature of the motor. This turns the shaft of the "Z drive" (shown above), which turns the ship's propellers. Click image for larger view and image credit.
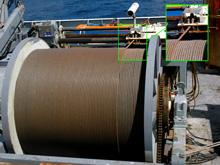
The WHOI Dynacon winch is fitted for DSL operations and has a hydraulic level wind on it that relies on three sensors for correct operation. The sensor that measures cable angle failed, causing the winch to fail to operate correctly. It was replaced and jury-rigged before DSL120 operations could be continued. This image shows the storage drum and level wind of the winch, displaying a larger view of the cable angle sensor. Click image for larger view and image credit.
DSL technicians stop the winch, freeze operations, and evaluate the problem. The misalignment appears to be due to a malfunctioning sensor. A magnetic sensor that detects and adjusts the cable angle as it is wound onto the winch storage drum failed. DSL technicians replace and readjust the failed sensor with a new one. The end of the day approaches and an atmosphere of relief permeate the ship until the technicians find that their last spare sensor fails too! One of the technicians figures out an innovative way to “trick” the sensor into working. Two major problems that might have sent the ship back to port are repaired, and equipment is back up and running properly. Everyday is a 24-hour workday and this Christmas day required overtime work of most of the ship’s technicians and engineers.
GalAPAGoS: Where Ridge Meets Hotspot will be sending reports from Dec 3 - Jan 10. Please check back frequently for additional logs from this expedition.
Sign up for the Ocean Explorer E-mail Update List.