Project Summary
In 2021, scientists and engineers at the Ocean Engineering Department of University of Rhode Island successfully developed and demonstrated a novel soft robotic system for underwater exploration with support from NOAA Ocean Exploration.
There are a great number of targets and objects on the seafloor and in the water column that ocean scientists want to interact with and/or sample. But scientists tend not to know ahead of time the exact shape and composition of these objects and whether they are fragile, brittle, hard, or soft. In this regard, soft robotics as an emerging technology is uniquely suited for grasping, manipulating, and sampling underwater. As compared with rigid metallic robots that may potentially damage or destroy delicate items when trying to grab them, the malleability of soft robotics allows scientists to interact with diverse marine environments more safely and effectively. Soft robotic systems also draw significantly less power and produce less acoustic noise than conventional hydraulic systems.
With the objective of engineering a programmable, hybrid manipulator that can be actively switched between soft/compliant and hard/rigid states, scientists and engineers at the University of Rhode Island built and tested two types of soft robotic grippers that will conform to an object's shape with light contact forces and pick up the object with the strength of a rigid claw. They tested and identified materials that give grippers neutral buoyancy to maintain their structural integrity in water. And they coupled these grippers with an electric drive, low-pressure hydraulic system that is “platform agnostic” - free from being tied to a specific platform and running equally well across platforms, including inspection-class remotely operated vehicles.
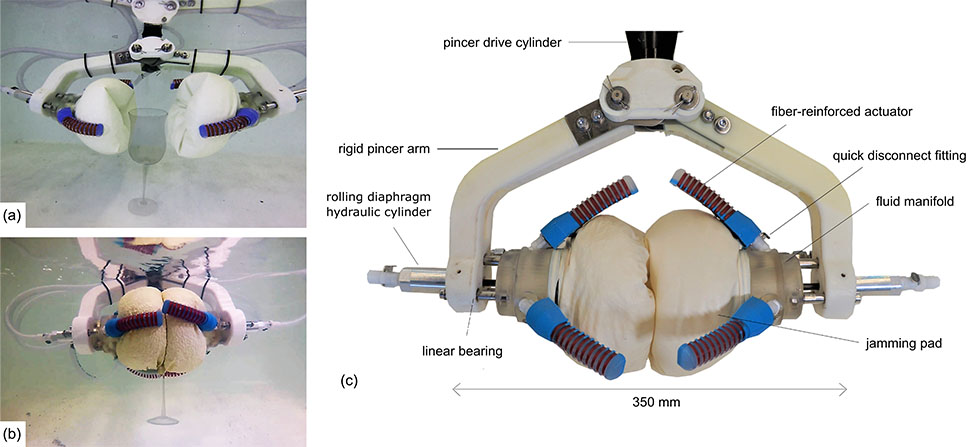
The scientists and engineers also applied the technology of additive manufacturing, commonly known as 3D printing, to produce soft robotic manifolds, actuators, and grippers that are more compact and easier to manufacture than previous designs. They used a commercial finite element analysis tool, known as Abaqus, to simulate the behavior of their gripper designs, thus improving their prototypes and assessing their performance with accuracy and cost-effectiveness before printing them. As a result, they also established a modeling approach for optimizing future gripper development.
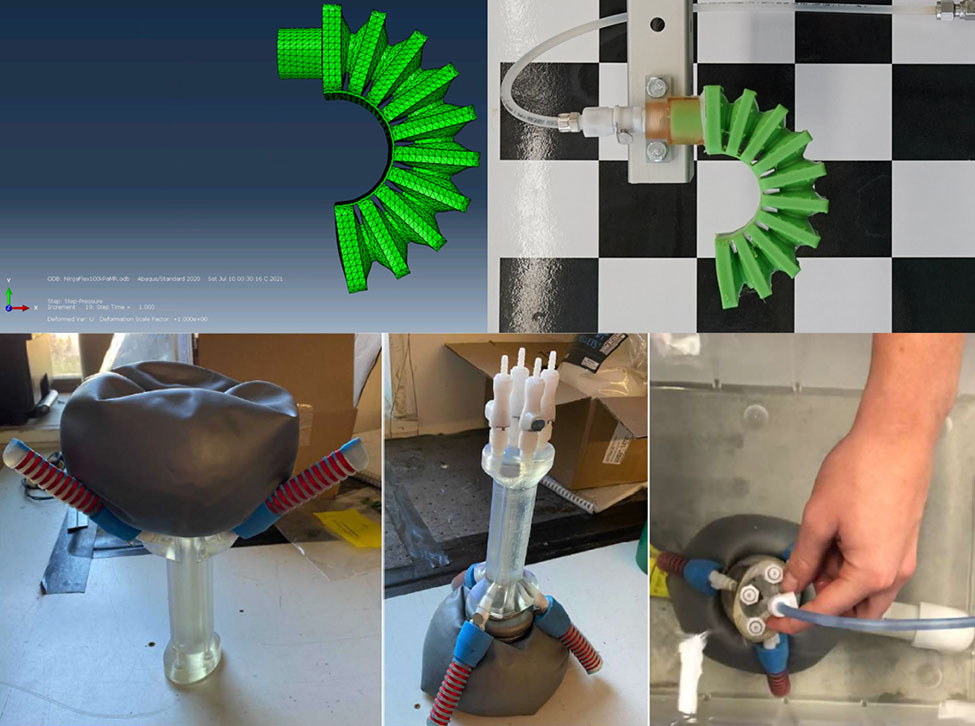
The scientists and engineers deployed and demonstrated the soft robotics they developed in shallow and deep water, interacting with different underwater environments in a flexible and dynamic way. The low component cost, low system complexity, ease of assembly, adaptability, and robustness all lend themselves to continuous research and development for advancing soft robotics design and its versatile application, including for marine archaeology and biology and ocean exploration in general.
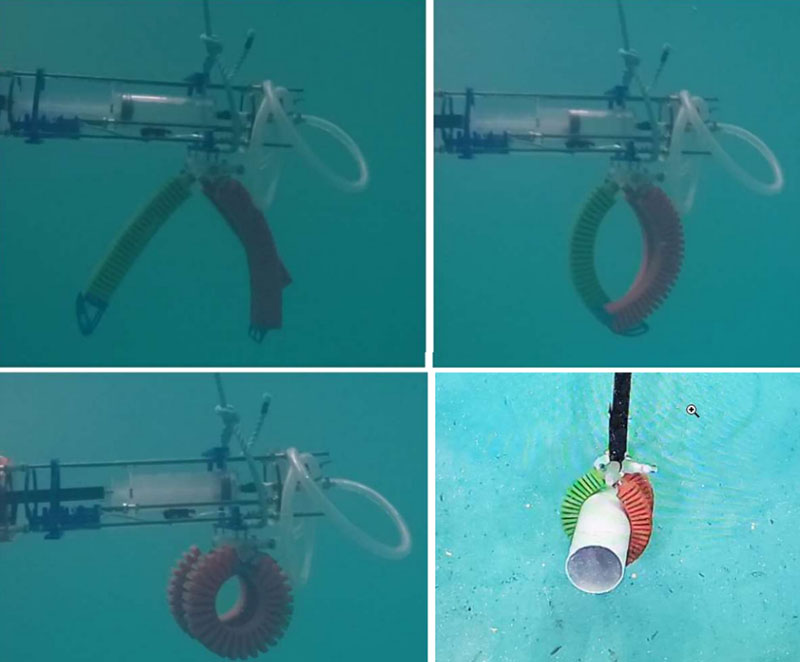
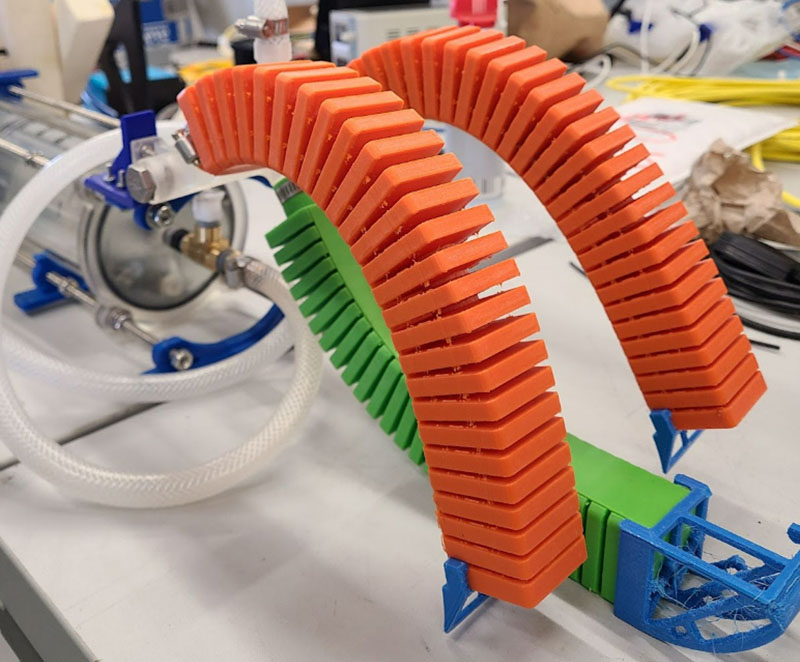
Contributed by Liang Wu, NOAA Ocean Exploration
Published October 31, 2022
Funding for this project was provided by NOAA Ocean Exploration via its Ocean Exploration Fiscal Year 2018 Funding Opportunity.